
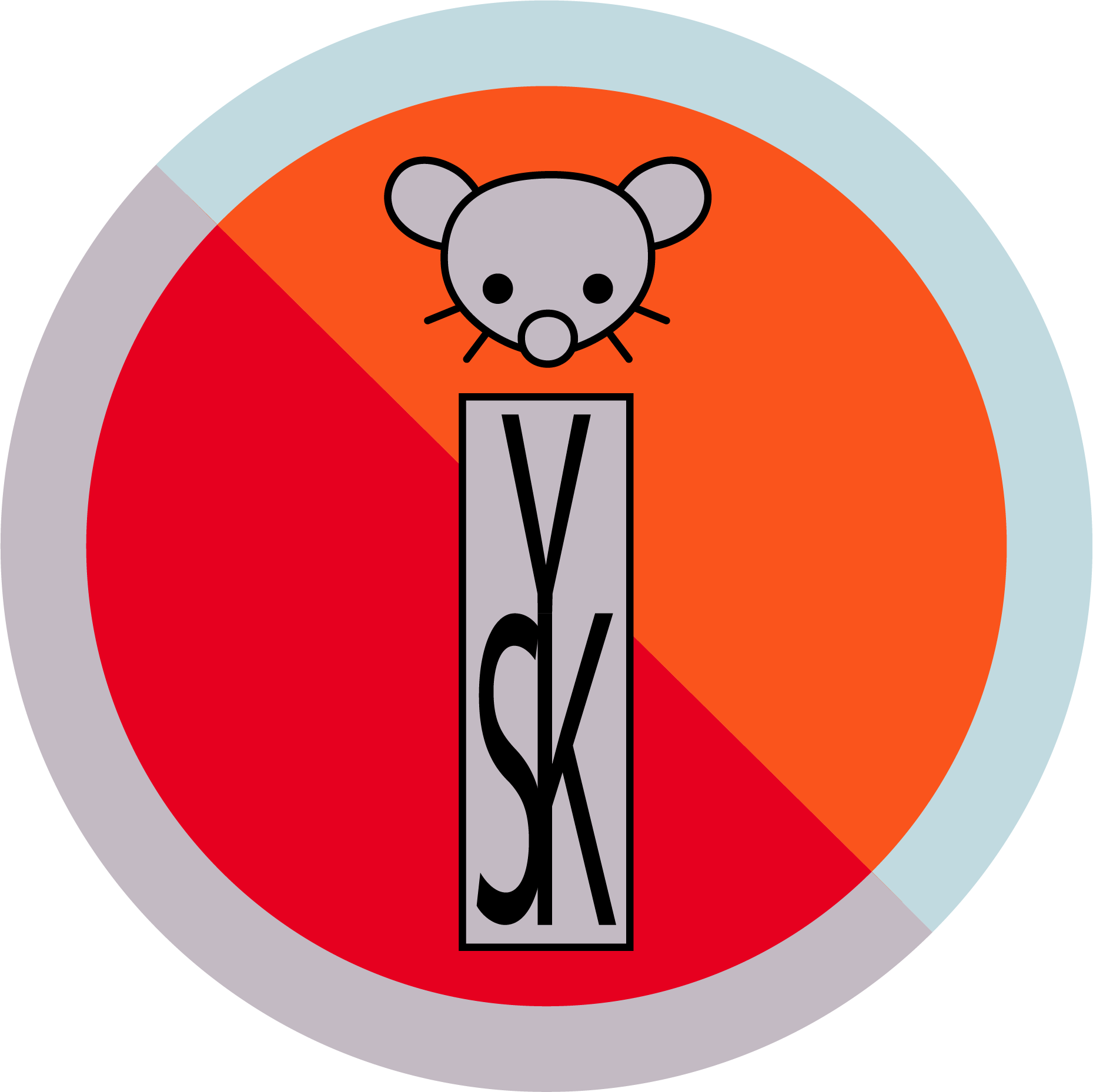
Me ordering a vegetarian meal in the airplane.
Woman yelling at cat.jpg
Me ordering a vegetarian meal in the airplane.
Woman yelling at cat.jpg
I hope aliexpress is better. I buy a lot of stuff from there like electronics components which aren’t really sold locally anymore. Also tools and arduino related things…
Ackschually, you don’t need to print them entirely sideways for structural integrity. Printing at an angle should also work and you don’t get so many artifacts from support material.
Can confirm. So far I’ve gotten an external monitor, keyboard, mouse, docking station and a stand for it so it can be used as a laptop as well while traveling.
It certainly has issues but it’s an impressive device.
I’m not particularly knowledgeable about IT but I avoid IoT like the plague. Everything should run locally and if I want to control it from away I’ll use a VPN to home.
Nice to hear! At the moment the spindle, if it has the right to be called that, is a 775 motor with a chuck attached to it. Which is good enough for circuit boards and wood. Perhaps aluminium is doable as well as long as the feed rate is kept slow enough.
Should milling steel ever be on the table I’ll make a larger machine and will use leadscrews on X and Y instead of belts and perhaps dual Z motors.
I’ve also designed the build around materials that were readily available such as the 18mm X rails. Apparently they’re quite obscure since they aren’t sold on typical Chinese webshops.
Thanks! Indeed the Z axis rests on only one MGN9H block. For stability it can be changed to two sliders per rail. For circuit boards and wood it should be strong enough to handle the load.
As for github/launchpad, I never used those before for sharing anything. I will look into those.
Nice! Once you get the hang of it FreeCAD is quite pleasant to use in my experience. I’ve updated the OP with a gdrive link.
I’ve designed it partially by importing step files of commercial parts such as the stepper motors, aluminium extrusions etc. They can be found on sites like grabcad. You can just make a throwaway account there since you need to sign up to download anything. At least it’s free…
I’ve updated the OP with a Google drive link.
I use a small hotplate at about 125 degrees and an aluminium baking tray. If you spread the beads out thinly it will dry pretty quickly.
Alternatively you can use an old microwave and that should remove moisture from the silica gel in a matter of minutes. You can easily overheat them though and I would never use that microwave for food again.
Can’t complain about that one!
Do you mean the steam deck?
I just use tweezers and a blue flame lighter. Heat it for 5 seconds then put it in the plastic. Then use the back of the tweezers as a flat surface to push it all the way in and level it.
This worked well so far and I really don’t see the need for a special soldering iron bit or a press like this.
I played it too.
I got an Orbiter 1.5 extruder and have been quite happy about it since. These days you’d be better off getting an Orbiter 2. As for the toolhead, there should be Ender 5 compatible mounts available on Printables or Thingiverse, if not you could design your own.
Creality also has its own direct drive, the Sprite Pro. That may be worth looking in to as well.
You can import a STEP model of both the Ender 5 and whatever mod you want to make to it and model your toolhead around it, that is what I did with the Mercury One project.
It’s worth the effort imo.
Bells frog big cherries jingle bells ham and cheese SEPHIROTH!
Swords in my knees… …Ed peed on this!
It’s not bad I would say. Right now I’m making a dedicated CNC for these kind of things and have the 3D printer just 3D print.
Here’s an example of a result from the laser cutter attachment.
And here’s a result of the plotter addon:
I have made something similar before for my Ender 5:
https://www.printables.com/model/1071387-ender-5-x-mgn12-detachable-toolhead-3d-print-laser
It’s definitely possible and the biggest challenge is making gcode that is compatible with Marlin. I’ve tried using gcode substitution commands in Prusaslicer as well as programs like FlatCAM and gotten good results out of it. You could indeed just tape it to the toolhead and set your home coordinates manually.
Try reading the gcode it produces. For cutting it should only have G1 X Y Z commands but it relies on a set home position.
You can set the home position in Marlin using G92 X0 Y0 Z0 and the run the gcode from there.
Overhangs are always difficult in 3D printing and your part cooling fan makes a huge difference in this. Also your print speed and temperature are factors.
This model however can also be printed sideways, you’ll have lower bed adhesion but it won’t have any overhangs this way.